January 18, 2025 by Bubaki Design
Computational Ceramic Forms
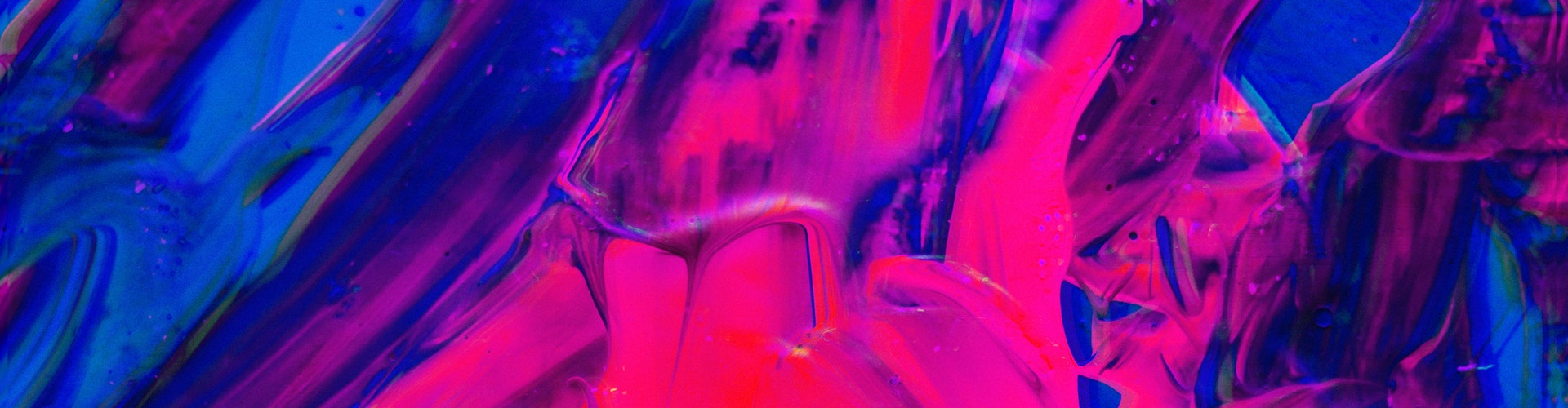
We’re exploring the intersection of digital form-generation and traditional ceramic processes, creating porcelain lighting elements that would be impossible to achieve through conventional pottery methods.
The Process
Using Blender’s generative capabilities, we design complex internal geometries and organic forms that challenge the boundaries of what’s possible in ceramics. These 3D-generated shapes become the basis for our slip-casting molds, allowing us to create porcelain objects with intricate hollow structures perfect for lighting applications.
The beauty lies in the dialogue between the computational and the handmade. While the forms are generated algorithmically, each piece requires careful consideration of material properties, wall thickness, and the physics of slip casting. We’re not just translating digital forms into clay—we’re discovering what new aesthetics emerge when traditional craft meets contemporary design tools.
Material Considerations
Working with porcelain presents unique challenges when dealing with complex geometries. We’ve been experimenting with:
- Wall thickness variation to create subtle light diffusion patterns
- Surface texture algorithms that translate to interesting glazing possibilities
- Modular systems where multiple cast elements can combine into larger installations
Current Explorations
Our latest pieces investigate how computational noise functions can create organic, coral-like internal structures that beautifully diffuse light while maintaining structural integrity. Each lamp becomes a unique luminous sculpture, where the interplay between form and function creates something entirely new.
This work represents our broader philosophy: using technology not to replace traditional craft, but to expand what’s possible when digital tools meet skilled hands and deep material knowledge.